How professional coating services help protect your equipment –
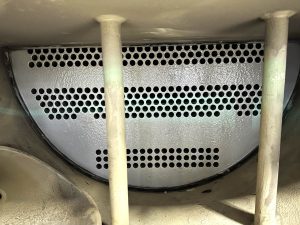
Inside the industrial evaporator we recently worked on, looking great for years to come. Photo by Colorado Coating Pros
It’s important to keep facility cooling systems running as long, and as efficiently, as possible. Ideally, a facility manager rarely needs to think about their chillers. But without faithful maintenance, this essential equipment can cause interruptions, costly repairs, lost productivity, increased energy bills, and even premature failure. An industrial cooling system will have a decades-long lifespan and a price tag to match. Your budget and your peace of mind will benefit from careful preventative maintenance.
In addition to regular cleaning, testing, and monitoring, be sure to watch for corrosion in your chiller systems, cooling towers, and return tanks. Condensation, chemicals, heat, abrasion, and exposure to the elements can all cause corrosion and compromise your cooling system. Professionally applied protective coatings can protect and preserve your equipment, ensuring the best efficiency and longest lifespan from your investment.
A new facility manager here in Colorado Springs called us recently when he discovered corrosion in their evaporators.
Understanding that corrosion can impact the lifespan and efficiency of their system, calling us was the best decision he could have made. Since we were still in the off-season, the customer was able to pull the endcaps off the evaporator without significant impact to operations. We cleaned up the corrosion and applied a protective barrier in just a couple of days that will protect these caps for years to come.
Our customer caught this corrosion early before it had a chance to significantly impact the system, but more advanced damage can be corrected as well. After sandblasting to remove rust and corrosion, and thorough cleaning, we repair any voids in the material with a high-grade epoxy novolac caulk and then coat with an expertly chosen epoxy formulation.
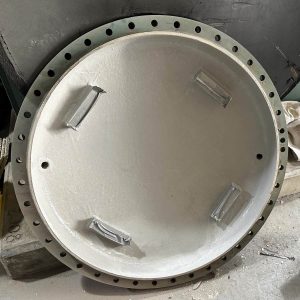
Better-than-new, freshly coated endcap. Photo by Colorado Coating Pros
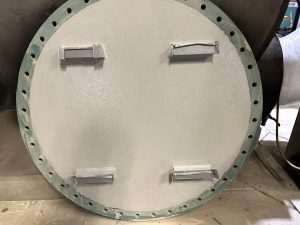
Ready for efficient operation, years into the future. Photo by Colorado Cooling Pros
For this job, we chose a specialty ceramic-filled solid polyamide epoxy coating. Engineered for harsh conditions, this coating provides excellent immersion performance, long-term wear protection, abrasion resistance, and no VOCs. The perfect choice to ensure this essential piece of equipment can effectively cool this facility long into the future.
Because our customer has a strong off-season maintenance plan, we were able to address his corrosion issues early on. He’s going into the cooling season with freshly coated, better-than-new caps on his evaporator tank, ensuring the highest efficiency from one of the biggest energy burdens in the facility. All without any interruptions in service.
He won’t need to worry about those endcaps anytime soon either. This epoxy coating is expected to perform for up to 15 years or more. Our experts choose the best quality coatings for each situation and our trained technicians do the job right the first time.
On your next system check, remember to look for signs of wear and corrosion on your cooling towers, chillers, and return tanks. Our experts can help keep your cooling system in tip-top shape, protecting your investment for years to come. Give us a call today.